SP-4 Dynamometer cell automation with built-in Closed-loop dynamometer
controller. The SP-4 dyno controller provides all the necessary
hardware and software for the control of an engine test bed, dynamometer
and combustion engine or rolling road dynamometers. The SP-4 is a fully
digital PID based closed-loop speed controller. It is the perfect tool for
engine performance testing, ECU calibration, endurance testing, emissions
etc.
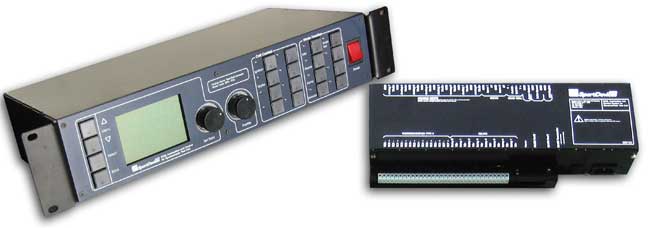
|
|
Features
- User-friendly operation thanks to the ergonomic design of
the console and flexible menu-guided parameter setting.
- Demand value setting via two incremental pulse encoders.
- Large LCD display for visualisation of demand values, actual
values and other parameters ´
- Control and monitoring of test engine and brake.
- Simple preparation and execution of tests.
- The controller will work stand-alone or connected through
our PC software.
- Remote control of dynamometer systems is possible (throttle
actuator, clutch actuator, gear shift, blowers etc.) from PC
software or console module.
- Test Modes
- n-constant (engine speed)
- Ramp test (programmable slope)
- Retarder (pre-programed load vs dynamometer speed) Ramp test
(programmable slope)SP4 has two selectable control modes. For
engine dynamometer applications, the selectable control modes
include:
- n-constant (engine speed)
- Ramp test (programmable slope)
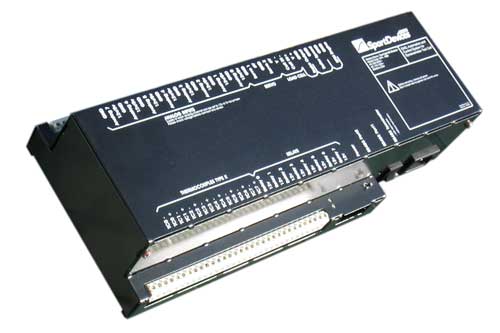
Input/Output Specifications
- 8 Analog inputs (0-5v)
- 8 Thermocouple (type-k) inputs
- 8 Digital outputs (Relays)
- 2 Servo outputs (Eg.Throttle, Clutch)
- 1 Load Cell input (16 bits accuracy and digital zero and
gain adjust)
- 1 PWM Brake Control Signal
- 1 Brake/Roller speed input
- 1 Engine Rpm Speed input
Power supply 3Kw, 192V
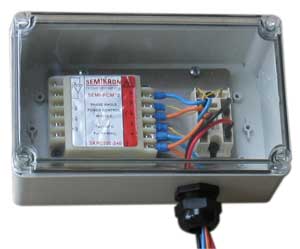
|
Load Cell
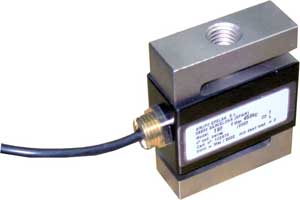
Available models: 15 kg, 30 kg, 60 kg, 90 kg, 150 kg,
225 kg, 450 kg ,600 Kg, 900 kg and 1500 kg.
Standard load cell model is 450 Kg. |
Typical installation:
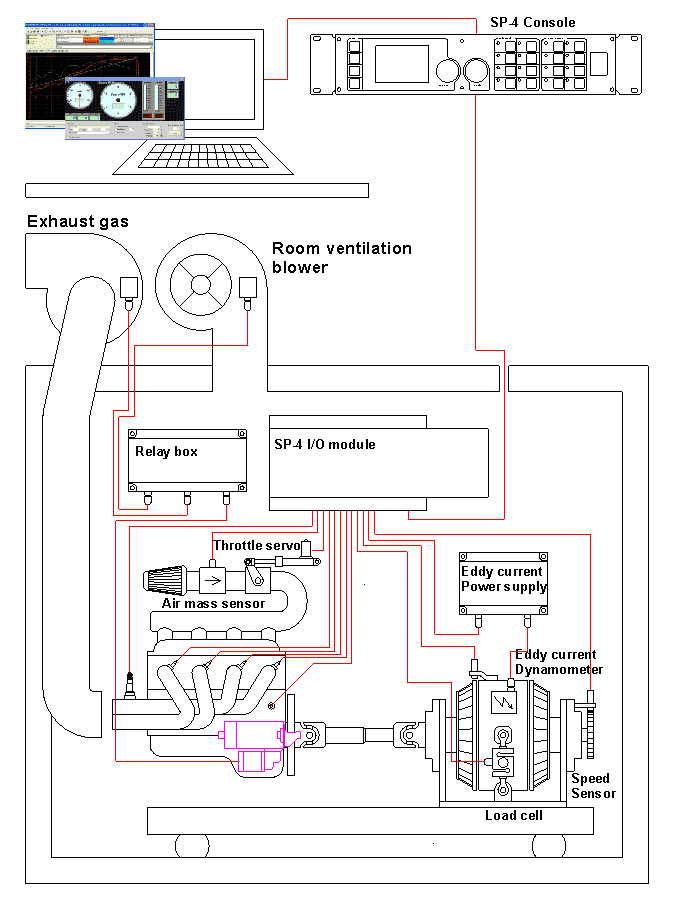
Part List:
- SP4 unit. It can work stand alone or with the computer.
- Computer. Pentium II or higher, Win98, ME, 2000 or XP.
- Hall Effect Sensor. Included with SP4.
- Gear Tooth. Installed on the eddy current brake to read its speed.
For example 8 teeth.
- Load Cell. It depends on the engine, typical values are 450 kg for
bike engines and 1000 kg for cars, but it should be calculated.
- Eddy Current Brake. 192 volt rated, it size
depends on the application.
- Power supply: Semikron control module + SCR & diode pack.
- Throttle Servo (optional). A high torque RC servo can be used to
drive the throttle.
- Ignition and Starter Relays. 12 volt relays to control the engine.
Additional relays can be installed on the SP4 to control the fans on the room.
- Fans / Turbines. Some type of fans or turbines are needed to next
functions:
- Feed the air intake with fresh air from outside the room (inner air gets
hot quickly) this turbine should be very high power (>2 KW, or >5KW) and
high speed to simulate on-track conditions, a variable speed driver is
recommended + frequency to voltage converter to use the brake speed.
- Exhaust extraction, the pipes should be made with iron or steel because
the high temperature of exhaust gas.
- Engine coolant, water should by couled by a fan, a car's fan or a
truck's fan can be used with a thermostat to ensure the water will be at a
right temperature.
- Engine and exhaust pipes cooling, when runing on the track the exhaust
pipes are being cooled as the vehicle runs, but when working on the dyno
they may get too hot and can be damaged. Certaint exhaust pipes can not work
at high temperatures (for example: titanium)
- Variable speed driver. It is recommended for air-intake turbine.
- Frequency to voltage converter. It converts the brake speed to a
voltage for the variable speed driver. Our F-V converter has a programmable
transfer curve to let the user to adapt the turbine speed to the brake speed as
he needs. An air speed sensor is recommended.
Photos of GSXR engine test bed:
     
|